Sample color matching
- Jessica Sweeney
- Dec 19, 2018
- 2 min read
Updated: Jul 12, 2024
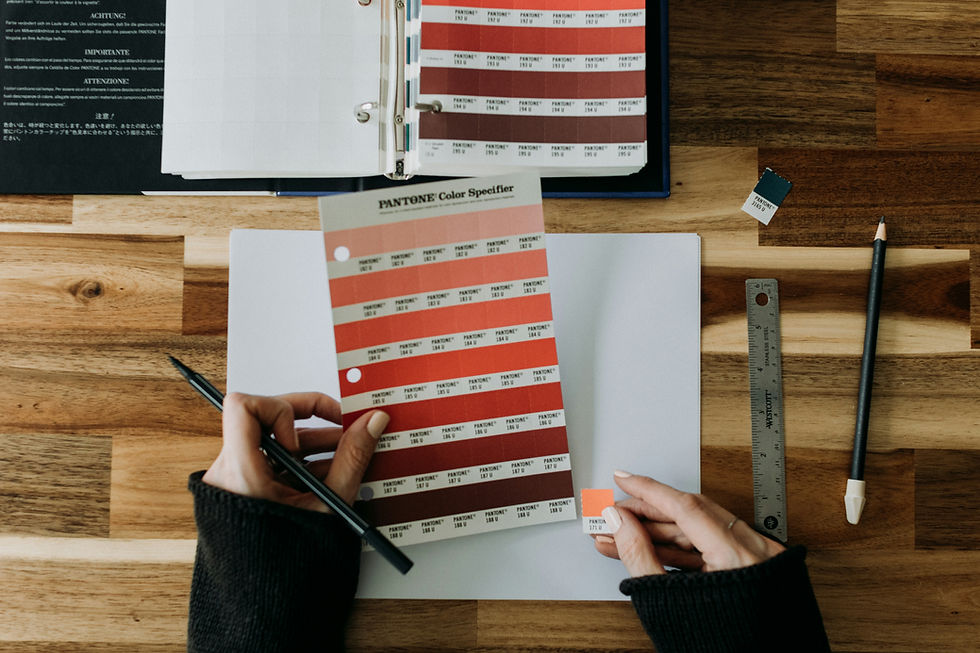
I wrote a post while back for Maker's Row about lab dips - https://www.developapparel.com/post/it-s-lab-dip-time . The process of lab dipping fabrics and trims to get them to match well is something that typically happens just before final product production. I have a couple of clients I'm working with lab dipping in the earlier stages of development to get some good looking photo samples to do product promotion to investors. First samples typically do not color match. A first sample is made to check the fit and function of the garment, see how the fabric handles in sewing and how it drapes on body. It's a good way to test the pattern, the sewing room or manufacturer stitch quality, and get a first estimate cost. Components for first samples are most often stock or available parts in the correct quality. The best way I've found to get around color matching and not having to lab dip on the first samples is to find contrast color parts that look good together. For example, a black zipper can work on an army green jacket or tonally similar parts can look nice too. I wish I took a photo of it, but I once got a neon green nightshirt with brown trims on it from a factory. That easily won the award for the least attractive first sample ever. It fit well, and the quality was great but it couldn't be shown to anyone without a bad reaction of "What is that!?".
So I don't leave you with an unattractive nightshirt visual in your head, here is a quick clip of some dyes being agitated at a factory.
Happy Holidays everyone!